Garagem360 visita fábrica de reforma de pneu de carga
O processo de reforma de pneus é bem popular no Brasil, tanto que o País é o segundo que mais presta esse tipo de serviço no mundo, ficando atrás apenas dos Estados Unidos. Os dados são da Associação Brasileira do Segmento de Reforma de Pneus (ABR), que também indica que o método proporciona uma economia de R$ 7 bilhões ao ano para o setor de transportes. Para saber sobre este processo, e como ele é feito, o Garagem360 visitou as instalações da SL Pneus & Auto Lins, em São Bernardo do Campo, São Paulo.
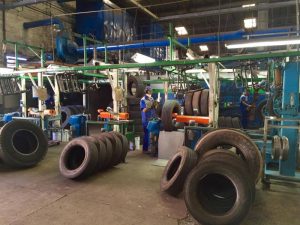
Reforma de pneus rende economia de R$ 7 bilhões ao ano para o setor de transportes | Foto: Maria Beatriz Vaccari/Garagem 360
Segundo Alexandre Levi, diretor comercial da empresa, que trabalha com pneus especiais para veículos de carga – eles reformam itens de 80% das empresas de ônibus, transportadoras e companhias de coleta de lixo da capital paulista -, o processo, se feito corretamente, é totalmente seguro e gera economia para as empresas (cerca de 25% a 30%, podendo chegar até 50%) quando comparado com a compra de um componente novo.
“Os pneus usados em caminhões chegam a ser os segundos ou terceiros itens mais caros de uma frota, mas a reforma permite que a companhia gaste menos dinheiro e reduza o custo das peças por quilometro rodado (preço do pneu dividido pela quantidade de quilômetros percorridos) e, consequentemente, o valor final das mercadorias”, afirma o executivo.
Na SL Pneus & Auto Lins, o valor cobrado pela restauração depende do modelo da borracha e do tipo de aplicação escolhida. Enquanto um pneu novo sai na faixa de R$ 1.500, os restaurados costumam variar entre R$ 450 e R$ 500. Por ser economicamente vantajoso e também mais ecológico, este serviço já é adotado por grande parte das empresas do ramo de transportes. De acordo com a ABR, o setor repõe mais de oito milhões de pneus das linhas caminhão e ônibus no mercado por ano.
Máquina digital raspa a camada de borracha (que será substituída) do pneu | Foto: Maria Beatriz Vaccari/Garagem 360
O processo
O primeiro passo do processo de restauração de um pneu é a limpeza. Depois que os componentes estão limpos, eles passam pelo exame de carcaça para detectar e pontuar danos. “Se estiverem muito deteriorados, não fazemos a reforma até por motivos de segurança”, diz Levi.
Depois, a peça é levada para a máquina de raspagem. Ela remove a camada de borracha que será substituída por uma nova. Um dos principais diferenciais da SL Pneus & Auto Lins é que o equipamento que faz esse processo é totalmente digitalizado. “Antigamente, o trabalho era feito manualmente. Agora, a digitalização permite um trabalho muito mais preciso e elimina erros”, explica o diretor comercial da empresa.
O próximo passo é chamado de “escariação”, e consiste em consertar “artesanalmente” os defeitos detectados na fase inicial. O objetivo é devolver a resistência original às partes danificadas, deixando-as aptas para aguentar a capacidade de carga e a velocidade. Na sequência, eles passam por outra máquina digitalizada para a aplicação de uma camada mais fina de borracha, que servirá como elo de ligação entre a carcaça e a nova “capa” externa.
Levi relata que a última aplicação de borracha (parte externa do pneu) pode ser feita de duas formas diferentes: anel e banda plana. A primeira consiste em cortar o material na medida do pneu e aplicá-lo manualmente. A segunda é considerada mais “refinada”, já que a borracha vem pronta em formato de anel. Por isso, ela não precisa ser cortada, e é aplicada sem emendas na carcaça por meio de um aparelho controlado digitalmente.
Sistema de anel aplica borracha sem emendas e tem como principal vantagem o balanceamento dos pneus | Foto: Maria Beatriz Vaccari/Garagem 360
“A principal vantagem do sistema de anel é o balanceamento dos dos pneus, pois a camada de borracha chega totalmente padronizada e com distribuição de peso igual em todas as partes da circunferência. Por ser fabricado em grandes quantidades, que depois serão divididas, fica difícil padronizar as medidas e o peso da borracha de banda plana. Dessa forma, os pneus acabam ficando mais “desbalanciados” graças à diferença de peso da borracha em cada uma de suas partes”, explica o executivo. Ele destaca ainda que a maioria dos clientes opta pela tecnologia de anel.
Com a borracha já aplicada, os pneus seguem para o processo de vulcanização. Eles são colocados em autoclaves (22 unidades por vez), onde ficam durante três horas e a uma temperatura de 115 graus para fixação e endurecimento.
Ao sair do forno, os itens passam por um novo exame para garantir que estão dentro dos padrões de qualidade. O último passo é a aplicação de uma camada de tinta a base de água para deixar o pneu esteticamente mais bonito. Ao todo, o processo demora cerca de um dia.
Informação digital e integrada
Além de deixar o trabalho mais prático e padronizado, o sistema tecnológico implantado no processo da fábrica da SL Pneus & Auto Lins permite que a empresa ofereça um serviço extra aos clientes. Com a digitalização dos dados, a companhia cria um banco de informações com os pneus de cada um. “Registramos relatórios com dados importantes como modelos, vida útil, dimensão e resíduo da borracha. O sistema também lista os principais motivos de recusa na hora da restauração, assim, é possível identificar os principais problemas encontrados nos pneus da frota e tentar minimizá-los”, finaliza Levi.